گریس چیست؟
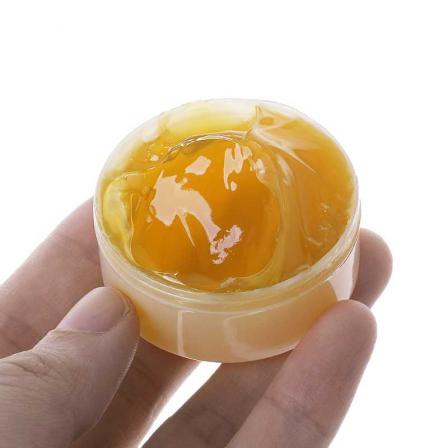
در این مقاله می خواهیم به سوال گریس چیست؟ پاسخ دهیم.
تعریف گریس
گریس یک ماده روان کننده به صورت جامد یا نیمه جامد است که از آمیخته شدن یک ماده پرکننده داخل روغن ساخته می شود. جهت بالا بردن این خاصیت، معمولاً از مواد دیگر نیز استفاده می کنند.
گریس از ترکیب چند صابون و مشتقات نفتی به همراه فیلر ها یا همان مواد پرکننده تشکیل شده که به صورت ماده جامد یا نیمه جامد برای مصارف خاص کاربرد دارد.
گریس یک ماده روانکار است که ساختارش متشکل از پرکننده می باشد تا به قطعات متحرک بچسبد و فشار و نیروی جاذبه باعث جدا شدن آن از قطعه ها نشود.
گریس ها نیز مانند روغن ها از نظر قوام و سفتی، با تقسیم بندی کلاس های مشخصی که از ۰۰۰ تا ۶ متغیر می باشد، ارائه می گردند. اندازه گیری این قوام و سفتی، با توجه به استاندارد خاصی تعیین می شود.
بدین منظور برای یک گریس با عمق نفوذ آن، از مخروط استاندارد و یک صفحه فولادی به صورت سوراخ دار تشکیل شده است و میزان قوام آن در دمای 25 درجه سانتی گراد تعیین می گردد.
انواع گریس که طبق این روش، گرید آنها با عدد های 000، 00 و 0 مشخص می شود، یک حالت ژله ای در دمای معمولی دارد که در بال برینگ ها و همچنین رول برینگ های سبک که شامل انواع مختلف مخروطی چند ردیفه، سیستم های روغن رسانی و گیربکس می باشند، کاربرد دارد.
برای گریس با گرید 5 و 6، باید بگوییم که در دمای اتاق بسیار سفت هستند و بیشتر به صورت بلوک های مستطیلی به بازار عرضه می شوند که موارد مصرف آنها در بال برینگ های چند پوسته ای ماشین آلات ذوب آهن و انواع کوره های چرخان و همچنین تجهیزات کاغذ سازی می باشد.
لازم به ذکر است که گرید 2 از آن جهت که بسیار نرم و روغنی هستند و تمامی احتیاجات مربوط به روغن رسانی در اکثر برینگ ها را برطرف می نمایند. همچنین جهت جلوگیری از ماسیدگی و افزایش ضریب اصطکاک و داغ شدن برینگ ها، از قوام و سفتی خوبی برخوردار هستند. به همین دلیل از متداول ترین و پرمصرف ترین نوع گریس می باشند.
و اما گریس گرید 3 کمی سفت تر از گرید 2 می باشد و بیشتر درباره بال برینگ های بزرگی که در محل نصب نیازی به روغن کاری ندارند و به خوبی درزگیری و آب بندی شده اند، کاربرد زیادی دارد.
بررسی کامل ساختار گریس
طبق آنچه که گفته شد، می توان به این نتیجه رسید که ویژگی ها و همچنین کیفیت گریس بستگی به نوع و مقدار تغلیظ گر، مواد افزودنی، مشخصات روغن پایه و فرآیند تولید آن دارد. یکی از ویژگی های مهم گریس، استفاده از آن در قسمت های غیر قابل دسترس در ماشین آلات به عنوان یک روانکار مناسب است.
ناگفته نماند که طراحی ماشین آلاتی که از گریس در آنها استفاده می شود، ساده تر می باشند و به تعمیر و نگهداری کمتری نیاز دارند. جهت آب بندی دستگاه ها نیز از آن بهره می گیرند. ولی با همه این مزایا، به علت ساختار ژله ای که دارند، توانایی انتقال حرارت و استخراج آلودگی از ماشینآلات را ندارند.
بدین منظور، ساختار گریس را اینگونه تعریف می کنند: یک ماده ژلاتینی به صورت جامد یا نیمه جامد که متشکل از روان سازی یا همان روغن های معدنی و یا سنتتیک و یک تغلیظ گر می باشد. در واقع گریس برای مواردی استفاده می شود که نیاز به غلظت بسیار بالایی باشد که روغن ها پاسخگو نمی باشند.
از موارد کاربرد آن می توان به یاتاقان های بزرگ، چرخ دنده های صنعتی و فلکه ها اشاره نمود. همچنین برای روغن کاری ماشین آلاتی که به طور مداوم از آنها استفاده نمی شود، کاربرد دارد.
گریس هایی که با کیفیت هستند، جهت روغن کاری قطعات به مدت طولانی مورد استفاده قرار می گیرند و کاربرد آنها برای درزگیری و افزایش طول عمر تجهیزات مختلف از جمله موتورهای الکتریکی و گیربکس ها می باشد.
از آنجایی که گریس ها از روغن پایه، تغلیظ گر و مواد افزودنی تشکیل شده اند، لذا مانند روغن ها جهت کاهش اصطکاک بین دو قطعه استفاده می شوند.
این ماده دارای ویسکوزیته بالایی است. به همین دلیل جایگزین بسیار خوبی برای مصارفی که روان کننده هایی مانند روغن در جای خودشان نمی مانند، می تواند باشد. این ماده روان کننده برای قطعات فرسوده قابل استفاده می باشد که باعث افزایش طول عمر این قطعات می گردد.
ماده تغلیظ گر یا سفت کننده، به عنوان حامل روغن می باشد و در حقیقت فقط روغن به انجام روانکاری می پردازد. بنابراین تفاوت اصلی گریس ها و روغن ها، وجود تغلیظ گر است. معمولا گریس ها بر طبق نوع تغلیظ گر، شامل پلیمر ها، صابون های فلزی و مواد معدنی می باشد و نوع روغن های پایه، به مینرال، سنتتیک و روغن گیاهی تقسیم بندی می شود.
در هنگام انتخاب یک گریس مناسب، باید طبق کاربرد و عملکرد آنها و بر اساس در نظر گرفتن یک سری فاکتورها این ماده روغنی با ارزش را خریداری نمود. به طور کلی ساختار یک گریس شامل سه بخش اصلی روغن های پایه، تغلیظ گر و ادتیو ها می باشند که در ادامه هر کدام را توضیح می دهیم.